SMED : Quanto tempo para trocar um pneu?
Como otimizar o tempo em que um processo não está produzindo? Conheça a metodologia SMED
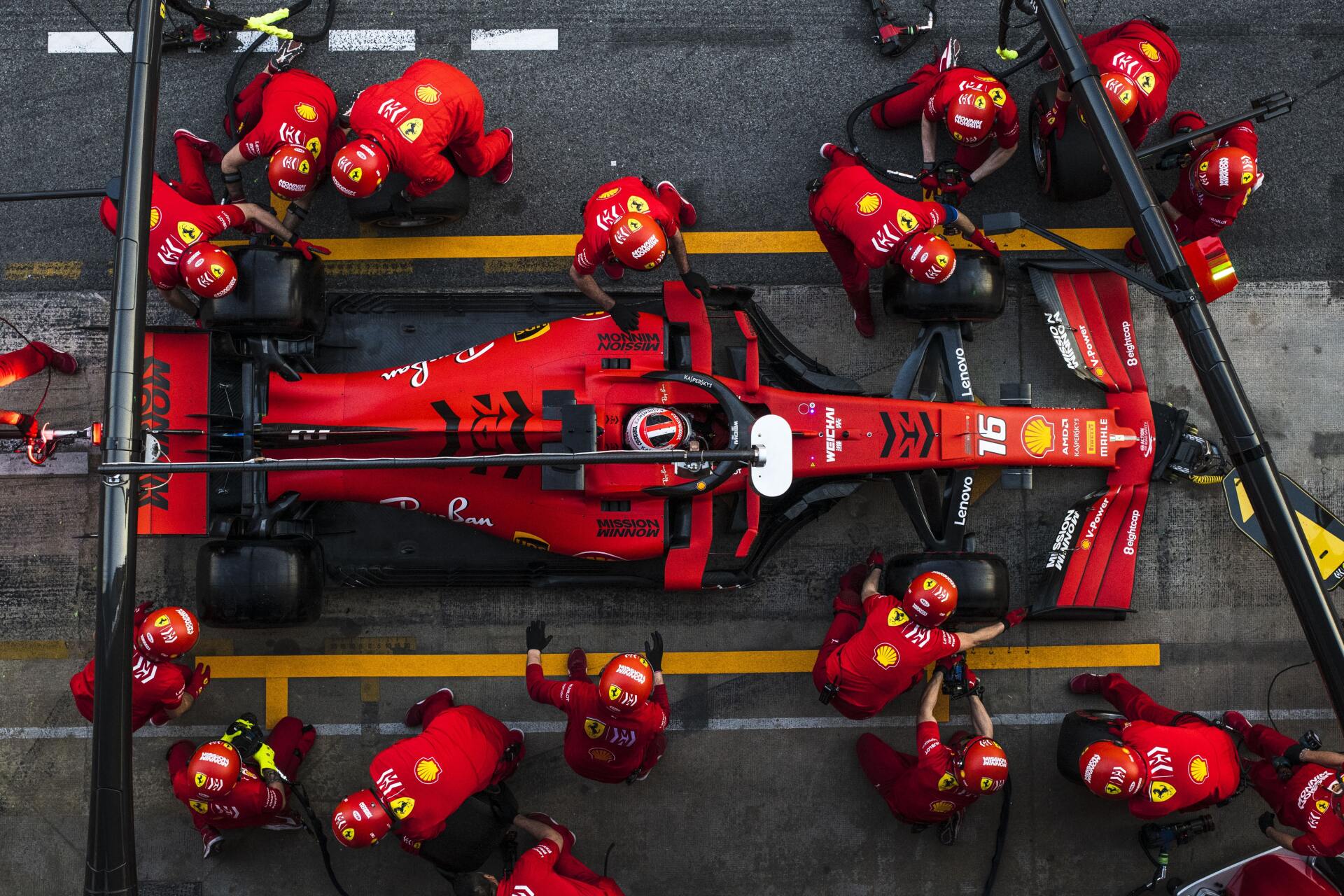
Quanto tempo você leva para trocar um pneu? Alguns minutos, talvez, mas que parecerão ter demorado uma eternidade, se você estiver a caminho de um compromisso importante. Se você for o Max Verstappen, pouco mais de dois segundos, vinte segundos no total se os tempos de entrada e saída do pit lane forem considerados. E que ironicamente também parecem uma eternidade. Voltando ao seu pneu, quanto tempo você vai demorar se o estepe estiver murcho ou se o macaco não estiver no porta-malas ?
Conheça a metodologia SMED, que possibilita a análise e otimização de atividades sequenciais. SMED é o acrônimo para “Single minute exchange of die”, que em tradução livre significa “troca rápida de ferramentas”. Os princípios da otimização dos tempos de setup (quando a “máquina” não está produzindo) remontam ao início do século passado, com a administração científica de Taylor. A metodologia SMED foi desenvolvida como parte do sistema Toyota entre os anos 50 e 70. Shigeo Shingo, o legendário consultor em otimização de manufatura, envolveu-se com a Toyota para a otimização dos tempos de preparação de prensas de estamparia. Ele desenvolveu e batizou o método, e foi o maior responsável pela sua difusão. Abraçado pelo movimento lean, o método é hoje utilizado para otimização de qualquer processo descontínuo.
O princípio do método é bastante simples: consiste em identificar as etapas que podem ser realizadas sem que o processo produtivo esteja parado (chamadas de
etapas externas) e executá-las previamente; analisar as etapas que exigem a parada do processo (etapas internas) e buscar formas de
reduzir seu tempo de execução (usando ferramentas mais adequadas, ou alocando recursos de forma mais inteligente).
Usando um pit-stop de Fórmula 1 como exemplo, toda a preparação ocorre antes de que o carro entre nos boxes: a separação dos pneus, o posicionamento da equipe, o sistema que controla a velocidade do carro no máximo permitido. Quando o carro para na posição, a execução ocorre separadamente em cada roda, cada uma contando com um mecânico pronto para retirar o pneu, outro operando a pistola e um terceiro com o pneu novo. Além disso, há uma coordenação geral da operação, há dois mecânicos operando o macaco, outro operando o "lollipop" para liberar o piloto, e mecânicos reservas com suas pistolas (a etapa crítica do processo).
Para chegar a este nível de otimização, SMED é a ferramenta estruturada ideal, e é importante que o workshop inclua as pessoas que executam as diferentes tarefas, e que o processo seja descrito tão detalhadamente quanto possível. A co-criação é muito importante para que se atinja o consenso de que é possível melhorar, já que tipicamente estes processos são simplesmente tomados por seu tempo total: “a parada para troca de ferramentas da máquina XYZ demora 12 horas”. Pode-se usar um diagrama de Gantt, e uma boa técnica é filmar o equipamento parado durante a intervenção, e convidar o time a observar as anomalias: momentos em que nada está sendo feito no equipamento parado (sinal de que atividades externas estão atrasando o processo), momentos em que uma peça está faltando ou que o operador está tendo dificuldades com uma ferramenta, ou fazendo sozinho algo que seria feito mais rapidamente em dupla. As ideias de melhoria são identificadas, priorizadas e executadas, e dentro do princípio da melhoria contínua, o exercício é repetido à medida em que novas anomalias vão sendo descobertas.
O impacto da aplicação da metodologia é impressionante, e Shingo dizia que sua base de dados de 1975 a 1985 mostrava uma redução de até 97,5% do tempo parado, o que é dramático se a unidade produtiva opera em sua capacidade máxima.
Posteriormente, o método passou a ser aplicado em outros tipos de processo descontínuo, e nós testemunhamos sucessos marcantes em operações tão diferentes quanto limpeza e manutenção de instalações industriais, otimização de operações batch na indústria química, operações de ponta na logística e até mesmo na otimização de processos administrativos. Ainda que não seja razoável esperar para qualquer tipo de processo uma redução tão importante quanto a relatada por Shingo, reduzir o tempo pela metade não é incomum, e é uma excelente forma de aumentar a capacidade líquida de produção, de forma rápida, barata e sem investimentos maiores.
Num exemplo que vivi pessoalmente, uma unidade de produção estava operando em sua máxima capacidade há anos, e a instalação necessitava de limpeza periódica para recuperação da capacidade. O melhor tempo histórico tinha sido de 40 horas, e um primeiro workshop SMED otimizou o processo para 22 horas. No primeiro teste do novo método, filmamos o procedimento e identificamos mais potenciais de melhoria, e o tempo foi reduzido para 12 horas, o que significa 30% do tempo inicial, sem afetar a qualidade da limpeza. A ação gerou uma capacidade adicional de 3,5 dias por ano, a custo praticamente zero.
Se você precisa aumentar a capacidade do seu processo,
fale conosco. A Zinneke encontrará o consultor ideal para seu desafio.
---
Eduardo Rocha acredita que metodologias como SMED são uma forma excelente de engajar equipes e obter resultados marcantes. É fundador da Zinneke
#SMED #melhoriacontínua #otimização
Photo by
Gustavo Campos on
Unsplash. Thanks!